○異なるフィルムを使用する工程での作業性とミスの改善
材質の異なるフィルムを複数枚重ねて熱プレスする工程にて、都度重ねる作業の手間が多いことや以下のようなオペレーションミスが頻発していました。
- 各材質1枚ずつ重ねる必要があるが、薄手のフィルムのため誤って2枚掴んでセットしてしまう
- 各材質を重ねる順番が決まっているが、順番を誤ってしまう
- 表裏を誤ってセットしてしまう
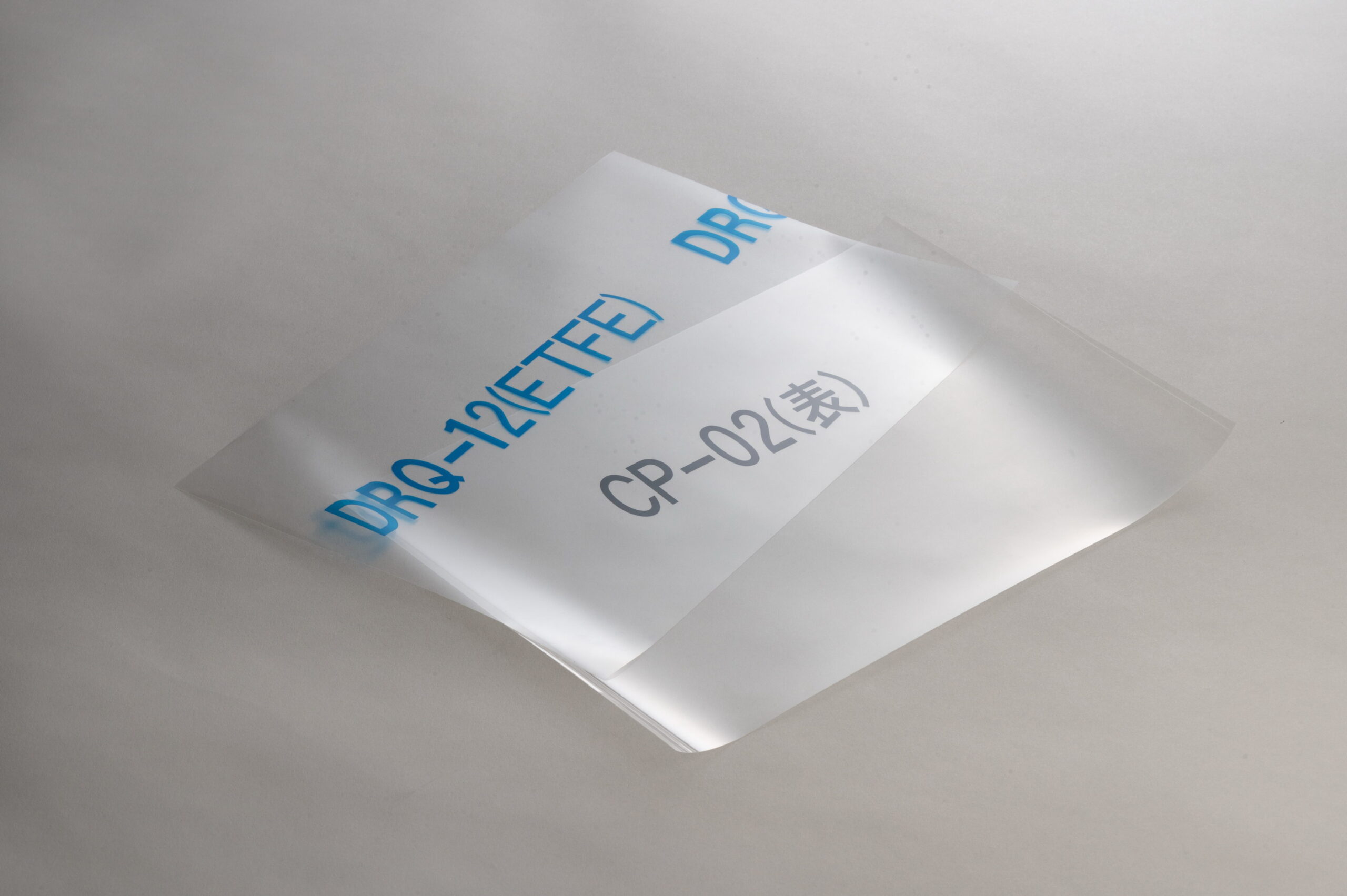
これにより製品不良が一定数出ていたため、お客様で運用方法の検討などによって改善を行ってきましたが限界がありました。また、単体のフィルムで厚みを薄くすることを検討しましたが、極端に薄いフィルムはハンドリングなど作業性の面からしても製造条件が安定せず断念していました。
そこで奥田では、材質の異なるフィルムをラミネートし一体化することを提案いたしました。
ご提案内容
まず、お客様が抱える複数の課題に対する解決策を提案しました。
- 重なる作業の手間、フィルムの2枚掴みや重ねる順番のミスなどの解決策として、フィルムをラミネートする
- 表裏セットミスに対する解決策として、表裏が一目でわかる印刷をする
- 作業性の兼ね合いで単体フィルムでは薄膜化が実現できなかったが、ラミネートすることで低(省)材料化を実現させる
この提案でお客様にご賛同頂けたため、現行の構成を維持したまま製品開発へ進みましたが、ラミネートしたことで特性に変化が生じ、品質を安定させることが出来ませんでした。また、ラミネート加工、印刷加工が加わったことでコストアップとなってしまいました。
そこで、奥田は更に工夫を行い、ラミネート後も要求品質を落とすことなく特性を維持するための厚みや安価な材質の調査、変更を行い、さらに生産性を向上させることでコストダウンを目指しました。
結果
複数回の試作、改良を行った結果、要求品質を維持出来ることがわかり、都度フィルムを重ねていた作業がなくなったことで生産効率が大幅にアップし、コストも下がるため採用に至りました。
また、量産後はオペレーションミスも劇的に改善されました。
副次効果として、フィルムをラミネートで一体化したことで複数製品の在庫管理や購買管理の手間を減少させることが出来ました。
異なる特徴を持つ素材を使用する工程でお困りなら
奥田へご相談ください!
奥田は製品の機能性向上やコストダウンだけではなく、作業工数を削減するためのご提案も可能です。
材料や製品の質は維持したまま、作業性の改善を実現できるように材料の調査や試作、改良を積み重ねます。
作業の手間やオペレーションミスでお悩みでしたら、ぜひ一度ご相談ください。